一、熱管
熱管是一種高效傳熱元件,利用全封閉的管內介質的沸騰吸熱和冷凝放熱進行熱傳導。熱管的導熱系數是金屬材料的數百倍乃至上千倍,它可將大量熱量通過很小的截面積遠距離地傳輸而無需外加動力。由于熱管具有導熱性能好、結構簡單、工作可靠、溫度均勻等良好性能熱管是傳熱領域的重大發明和科技成果,給人類社會帶來巨大的實用價值。
熱管的特點:
由熱管組成的換熱器換熱效率高,結構緊湊、流體阻力低;單根熱管損壞對設備換熱影響不大,即使部分熱管損壞也不會影響設備的正常運行;可以調整冷熱端的換熱面積控制管壁溫度,避免露點腐蝕。熱管換熱器已廣泛應用于化工、冶金、建材、能源等行業熱能設備的余熱回收工程中。
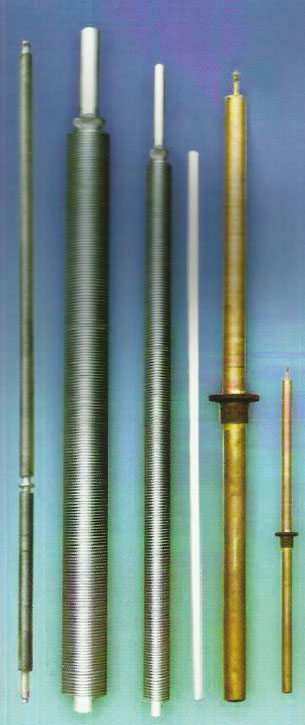
熱管的分類:
根據熱管工作溫度不同,熱管可以分為高溫熱管(工作溫度在450~1000℃) 、中溫熱管( 工作溫度在250~450℃)、常溫熱管(工作溫度在0~250℃ )和低溫熱管(工作溫度在-273~0℃ ) 。熱管工作溫度不同采用的熱管工質也不同,高溫熱管通常采用液態金屬鈉等, 中溫熱管采用苯、導熱姆等有機物, 常溫熱管采用水、乙醇等,低溫熱管采用氟里昂等。
熱管的控制原理:
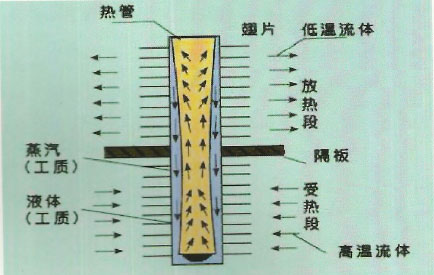
對重力式水-碳鋼熱管,構造上可以分成加熱段和冷卻段兩部分。工作時,熱管的加熱段換熱面從高溫煙氣吸收熱量,使熱管內部的液態水沸騰變成蒸汽,蒸汽上升到冷卻段后,受冷水冷卻而重新變成凝結水,放出汽化潛熱。然后在重力作用下,凝結水返回加熱段繼續吸熱,完成一次工作循環,如此循環往復,介質不斷地把熱量由煙氣傳遞給冷卻介質。
熱管的應用:
熱管技術被公認是一種很有價值的傳熱新技術,在空間技術、電器工業、核電工業、化學工業、食品工業、動力機械、冶金工業余熱回收等很多方面都得到了廣泛應用。
我公司生產的熱管換熱設備已經有十余年的歷史,生產了近千套熱管換熱器,換熱形式有氣-氣型、氣-液型等。
1、氣-氣型熱管換熱器
冷熱氣流均為氣體,熱管兩側均饒有翅片,以強化傳熱。
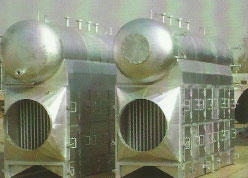
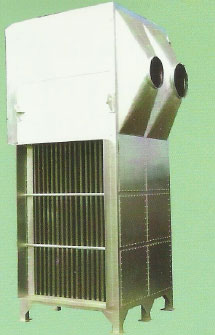
2、氣-液型熱管換熱器
熱流體為氣體,冷流體為液體。熱管將熱量傳送給水,可以生產中、低壓蒸汽。
二、燒結余熱利用隨著工業的高速發展和人類生存環境的惡化,節能減排工作已經得到世界各國政府的高度重視。十七大以后,我國各行各業都十分重視節能減排技術。如何利用工業生產中產生的廢氣余熱余能資源已經成為人們研究和實驗的課題。
鋼鐵工業是耗能大戶,其能耗占全國總能耗的10% 以上。鋼鐵工業是各種節能減排新技術推廣應用的重要用戶。
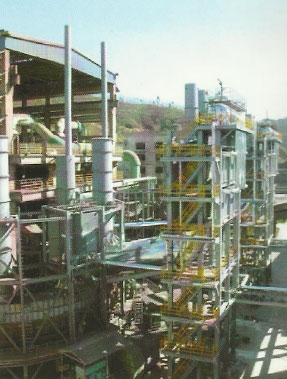
燒結工序:
高爐礦料入爐以前的準備工序,其能耗占鋼鐵生產總能耗的12%,燒結在生產過程中排出了大量含粉塵的熱廢氣,其排放的余熱約占燒結總能耗熱能的50%,造成二次能源的浪費,嚴重污染環境。由于這些廢氣溫度不太高,含塵量大,廢氣量特大,熱廢氣的利用尚未得到普及。回收利用這些煙氣余熱極為重要。在燒結工序內,廢氣溫度從450℃逐漸降低到150℃一下。高溫部分溫度在300~450℃,根據測量結果,這部分廢氣占整個廢氣量的30%~40%;低于300℃的廢氣量占所有冷卻廢氣量的60%以上。
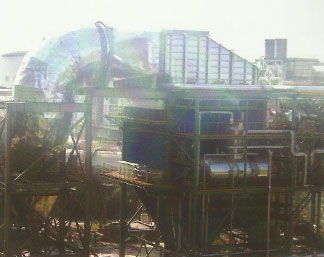
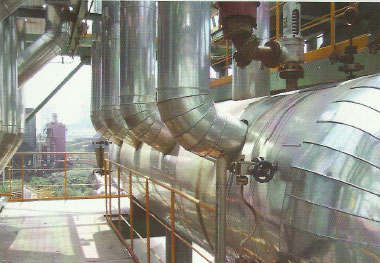
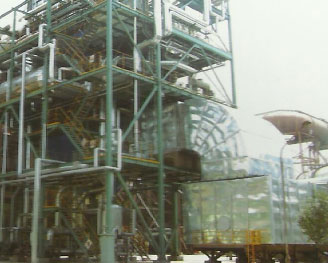
燒結余熱利用的方法:
將燒結的環冷機或帶冷機高溫段煙氣抽出先經過擋板式除塵器凈化,然后送入余熱鍋爐加熱經除氧過的軟水,生產具有一定壓力和溫度的蒸汽。這些蒸汽可以達到壓力1.6MPa、溫度260℃,直接供生產或者供汽輪機使用以帶動發電機發電。被余熱鍋爐冷卻后的煙氣去向有兩種方式
可供選擇:
方式1.經引風機的抽引送回到環冷機或帶冷機高溫段下部風箱再次冷卻燒結礦。即這部分煙氣周而復始地循環,不斷地將燒結礦的顯熱帶給余熱鍋爐生產蒸汽。方式2.被余熱鍋爐冷卻后的煙氣經引風機抽引后送進新建的煙囪直接排放到大氣。
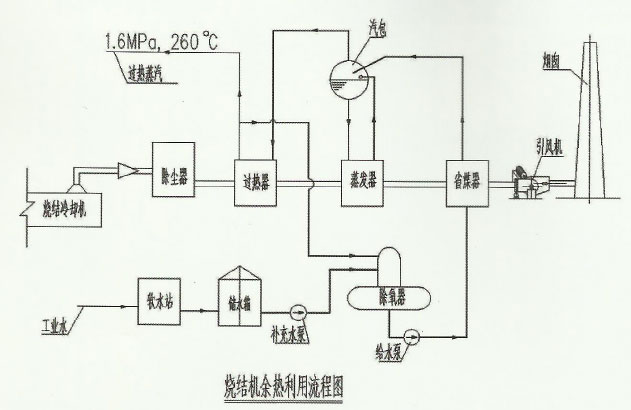
方式1 的優點是可以使進余熱鍋爐的煙氣溫度提高20℃左右,多產生一部分蒸汽。缺點是引風機全壓必須提高,即電耗必然增加。其次是水平煙道占地多一些。方式2 的優缺點與方式1 相反,在余熱鍋爐的附近布置給水泵、加藥裝置、補充水泵和儲水箱。如果不需要發電,余熱鍋爐生產的蒸汽便可以直接輸入外部蒸汽管網供全廠生產使用。如果需要發電,在距離余熱鍋爐不太遠的空地建造發電站,站內布置汽輪機、發動機及其輔機設備。在發電站的附近布置汽輪機循環冷卻水的冷卻塔。關于燒結機余熱利用的關鍵設備—余熱鍋爐的選型,推薦采用煙道式余熱鍋爐。
三、電爐煙氣余熱回收節能減排是當前社會發展的主題,,煙氣余熱資源的回收利用是節約能源和減少污染的有效途徑之一。電爐冶煉在我國鋼鐵企業相當普遍。其生產過程中一方面要消耗大量的能源,另一方面電爐冶煉過程中產生的大量熱量隨煙氣排出,既污染了環境,又造成二次能源的極大浪費。因此如何更好地回收利用這部分煙氣余熱資源,是我們面臨的重大技術課題。
電爐煙氣系統的流程:
從電爐爐口被吸入煙道的空氣與煙氣中的CO燃燒后,使煙氣溫度達到1000至1400℃。高溫煙氣在煙道內首先進入沉降室,煙氣中大顆粒煙塵因重力作用沉降后進入水冷煙道進行熱交換降溫,使煙氣溫度降到200℃左右,進入布袋除塵器除塵,最后由引風機經煙囪排入大氣。電爐的高溫煙氣通過水冷煙道的換熱冷卻,出來的熱水再送回到冷卻塔冷卻后再循環使用。煙氣的余熱資源不但沒有回收利用,水泵還要消耗大量的電能,造成較大的能源浪費。只有在煙道沉降室的口設計安裝余熱利用裝置(即余熱鍋爐),代替原有水冷煙道,這樣才能既充分回收電爐煙氣的顯熱生產蒸汽,又能降低煙氣溫度,保護袋式除塵器。其生產的蒸汽可供應全廠生產使用,也可以用于帶動發電機發電。電爐在冶煉過程中,排放出的煙氣流量、溫度、含塵量呈現周期性地變化。冶煉期的煙氣溫度最高,流量最大,含塵量多,在出鋼和兌鐵水
期間沒有煙氣。
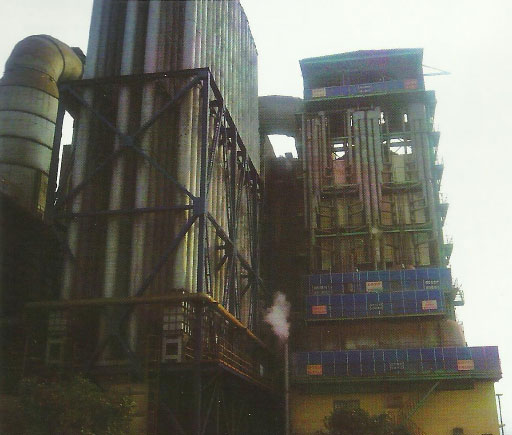
為了適應電爐在整個冶煉過程中煙氣量巨大的變化,可以選用兩種余熱鍋爐中的一種:(1)熱管式余熱鍋爐;(2)補燃式余熱鍋爐。
目前有的鋼鐵廠采用了啟動性能快,等溫性能好的熱管作為余熱鍋爐的傳熱元件。即熱管式余熱鍋爐。由于高溫熱營造價很高,故采用中、低溫熱管(即碳鋼水熱管)比較經濟實用。
(1)熱管余熱鍋爐:
熱管余熱鍋爐系統主要由高、低壓蒸發系統、除氧器、蓄熱器、補充水泵、給水泵、儲水箱、閥門以及監控儀表等組成。高壓蒸發系統由高壓汽包、下降管、省煤器、高壓熱管蒸發器和上升管組成。低壓蒸發系統自低壓汽包、下降管、低壓熱管蒸發器和上升管組成。
低壓蒸發系統生產的蒸汽供給蹤氧器加熱補充水—熱力除氧。高壓蒸發系統產生的高壓蒸汽(1.8MPa的飽和蒸汽)輸送給蓄熱器。蓄熱器工作壓力和輸出蒸汽的流量和溫度也隨著電爐在冶煉過程中煙氣量的斷續變化而波動。
從傳熱的性能,熱管余熱鍋爐是適合于電爐煙氣斷續變化的工況。但是,即使設置了蓄熱器,其外供蒸汽的流量,溫度和壓力也是變化的,而且是飽和蒸汽。由于熱管元件傳熱性能的衰減,一般在5 年后,其蒸發量和蒸汽壓力都會有較大地減少。
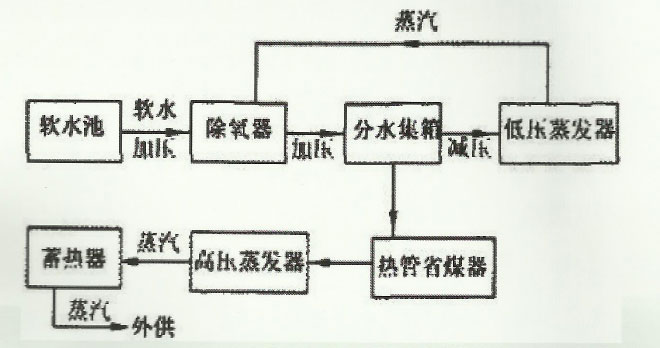
(2)水管式余熱鍋爐:
我公司設計人員經過多年的研發,采用正規水管式余熱鍋爐,利用電爐高溫煙氣顯熱生產連續穩定和溫度都較高的蒸汽,供全廠生產使用或者供發電使用。該類余熱鍋爐具有熱效率高,使用壽命長的特點(確保20 年以上)。
四、高爐熱風爐雙預熱裝置衡量高爐冶煉技術是否先進的技術指標主要有兩項:(1 )風溫指標;(2) 噴煤指標。高風溫、大噴煤量是高爐降低焦比,降本增效唯一最有效的方法。要增大噴煤量也必須首先要提高風溫。所以提高風溫對于提高高爐冶煉技術的先進性尤為重要。
要確保風溫的提高可選擇以下兩種方法中的一種。方法( 1 )在進入熱風爐燃燒的高爐煤氣中摻燒部份高熱值煤氣(例如焦爐煤氣) 增加混合煤氣的低位發熱值;或者方法(2) 提高進熱風爐燃燒的助燃空氣和高爐煤氣的初始溫度,增加其物理熱。因鋼鐵廠焦爐煤氣都十分欠缺,而高爐煤氣卻相對富裕。所以大部分鋼鐵廠采取了方法( 2 )。熱風爐在全燒高爐煤氣的條件下,僅管一般高爐都采用了煙氣余熱利用技術。即利用熱風爐排出的煙氣顯熱加熱助燃空氣和高爐煤氣以提高其初始溫度( 150 至170℃)。但是對提高風溫非常有限,一般只能達到1000至1050℃。
所以國內外不少高爐,為了使送風溫度達到1100至1250℃,甚至1310℃,都采用了設置前置燃燒爐產生高溫煙氣,將助燃空氣和高爐煤氣加熱到更高的初始溫度。這一設置前置燃燒爐的方案有兩種加熱方式:(1)兩級分段式加熱方式;(2)一級加熱方式。
(1)兩級分段式加熱方式:
第一級加熱是設置熱風爐煙氣余熱利用裝置,即由空氣換熱器和煤氣換熱器組成。它們分別把空氣、煤氣預熱到150-170℃。第二級加熱裝置是由前置燃燒爐、空氣換熱器、煤氣換熱器、煙氣引風機、鼓風機和各類閥門等組成。利用前置燃燒爐燃用高爐煤氣獲得高溫煙氣,再摻入第一級余熱利用裝置排出的部分熱風爐煙氣,使前置燃燒爐排出的混合煙氣溫度達到700至800℃。然后進入兩臺換熱器分別進一步加熱助燃空氣和高爐煤氣。一般將高爐煤氣加熱到250至300℃;將助燃空氣加熱到450至550℃。便可以大幅度提高熱風爐的爐膛燃燒溫度,使拱頂溫度達到1450℃以上,從而確保送風溫度達到1100至1310℃的效果。第一級加熱裝置可以采用管式換熱器;也可以采用熱管式換熱器。第二級加熱裝置,因為煙氣溫度太高,采用管式換熱器為宜。
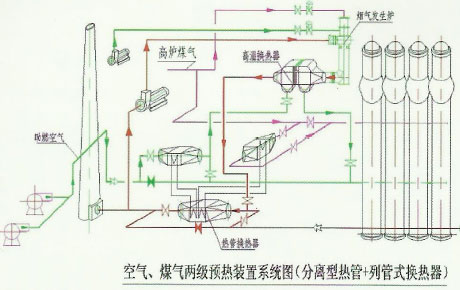
(2)一級加熱方式:
針對方式( 1 )兩級分段式加熱方式有4臺換熱器或者3 臺換熱器(高爐煤氣只進行一級加熱時),設備和大直徑管道較多,現場難于布置。為此,產生了一級加熱的方式,這種加熱方式仍然由前置燃燒爐、空氣換熱器、煤氣換熱器、煙氣引風機、鼓風機和各類閥門等組成(沒有了第一級加熱的兩臺換熱器)。前置燃燒爐燃用高爐煤氣獲得高溫煙氣,再摻入熱風爐排出的部分煙氣,使兩者煙氣混合為700至800℃。然后進入兩臺換熱器分別加熱助燃空氣和高爐煤氣。為了使高爐煤氣加熱到250至300℃、助燃空氣加熱到450至℃,必須根據上述要求的溫度值計算和
設計兩臺換熱器的換熱面積。這種前置燃燒爐加一級加熱方式的兩臺換熱器也只能采用管式換熱器為宜。
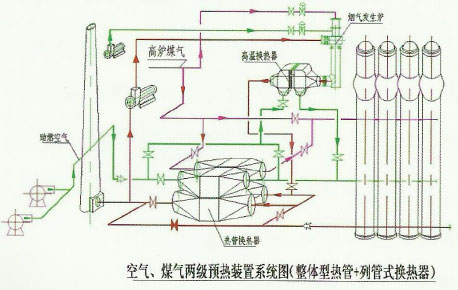
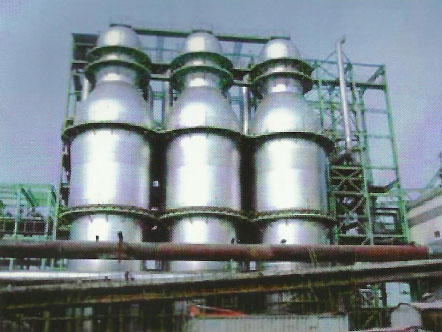
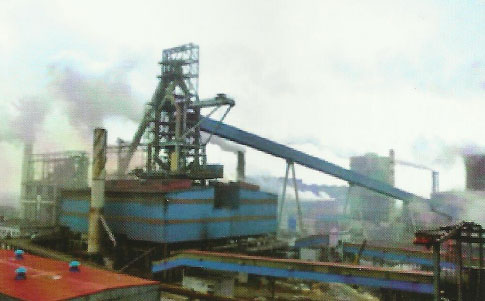
工藝特點:
●熱風爐在單燒高爐煤氣條件下,實現送風溫度達到1200-1250℃以上;
●操作簡單、運行可靠、可隨意調節空氣、煤氣預熱溫度、滿足生產需要;
●占地面積小、維護量小、不需要增加操作人員;
●設備可靠、壽命長、可保證一代壽命達到10年以上;
●經濟效益顯著、投資回收期短(約3-6個月)。
五、焦爐上升管荒煤氣余熱利用焦化行業作為高能耗行業,被國家列為落后產能企業。在國家大力鼓勵節能降耗先進技術開發應用的緊迫形式下,我們成功設計了焦爐上升管荒煤氣余熱利用裝置。
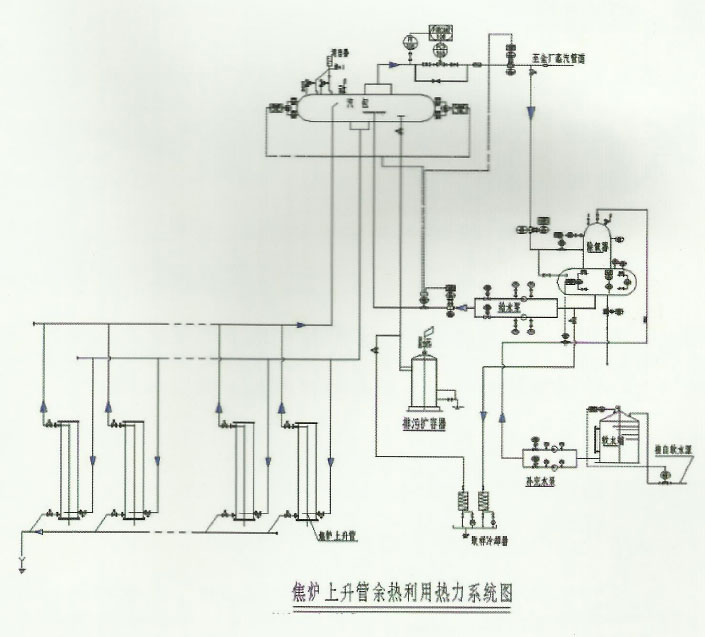
離開焦爐碳化室進入上升管的荒煤氣溫度高達750℃以上,每個上升管荒煤氣流量超過400Nm3/h,一座焦爐有幾十個上升管。即現狀是大量的高溫荒煤氣離開上升管后進入集氣管用氨氣冷卻,不但消耗大量的氨水,而且浪費大量的二次能源。現在我們把上升管設計為軟水蒸發器(取代原有襯磚型上升管)。一座焦爐有幾十個這樣的蒸發器,再加上具有汽水分離作用的汽包和除氧器、給水泵、補充水泵、儲水箱以及熱工監控儀表等組成了焦爐上升管荒煤氣余熱鍋爐系統。
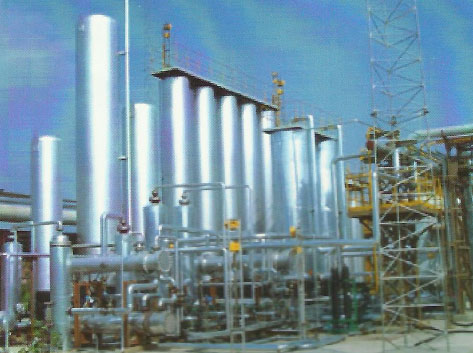
外部管網提供的軟水首先存入儲水箱,然后軟水由補充水泵升壓后注入除氧器被加熱除氧。除氧后的軟水由給水泵升壓注入汽包。汽包中的欠熱水由下降總管、支管輸送給每個荒煤氣上升管。上升管內的部分水吸收荒煤氣顯熱變成蒸汽,與未汽化的飽和水組成汽水混合物離開上升管經支管、總管再進入汽包。汽包中的蒸汽經汽水分離器脫水后由飽和蒸汽總管輸出,供給生產或生活使用。一座焦爐幾十個上升管每小時可以生產0.8MPa的蒸汽5 至7 噸。按平均6t/h計算,1 年可以生產蒸汽52500 噸。年均節約標準煤5518 噸,減排CO2共計12100噸。工程項目總投資約3 年可以收回。
焦爐上升管荒煤氣余熱鍋爐(含汽水系統管路)以及控制系統都嚴格按照國家勞動部頒發的《蒸汽鍋爐安全技術監察規程》設計、制造和施工,確保2 5 年不得漏水。即整個上升管余熱利用裝置的使用年限與焦爐爐齡基本相同。
六、軋鋼加熱妒余熱利用軋鋼加熱爐有多種形式。盡管都燃用煤氣,但其排煙溫度各不相同。-般在250至600℃范圍內。加熱爐排出的煙氣量也各不相同,一般在20000至80000Nm3/h。對于溫度高(例如350℃以上),流量大(例如30000 Nm3/h以上)的加熱爐都應設置余熱鍋爐加以利用——生產蒸汽供應鋼鐵生產使用或者供應發電。軋鋼加熱爐的煙道一般都在地下室內。其煙道兩旁空余位置都比較少,將余熱鍋爐布置在煙道附近是非常困難的。最好是在地下煙道適當的位置開孔接出一根新設置的煙道到地面上,將加熱爐煙氣引入到布置在地面上的余熱鍋爐內。在地下煙道接口附近的新煙道上設置一個煙氣調節閥和一個煙氣切斷閥。設置煙氣調節閥的目的是為了控制軋鋼加熱爐爐膛壓力能夠保持余熱回收前的微正壓,絕不影響軋鋼工藝生產。在余熱鍋爐附近布置煙氣引風機、煙囪、給水泵、加藥裝置、補充水泵和儲水箱。
軋鋼加熱爐余熱鍋爐可以選用單壓鍋爐加上除氧器的組合形式;也可以選用雙壓鍋爐的形式(不要單獨設置除氧器)。雙壓鍋爐的低壓汽包兼有除氧器的功能。
雙壓鍋爐的汽水循環流程如下:由余熱鍋爐、除氧器、水泵、閥門和連接管道組成了汽水循環系統。儲水箱中的軟水由補充水泵增壓注入余熱鍋爐的低壓省煤器余熱到60℃左右,再進入除氧器,即低壓汽包。被除氧后的水由除氧器下部出水管引出分為兩路:一路由管道輸入余熱鍋爐低壓蒸發器。由煙氣加熱為低壓汽水混合物后(自然循環),再進入除氧器。另一路由給水泵增壓注入余熱鍋爐高壓省煤器,被煙氣加熱到150℃左右進入余熱鍋爐汽包。汽包中的水由下降管導入高壓蒸發器。由煙氣加熱為高壓汽水混合物再進入汽包。
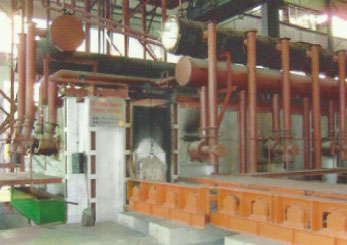
除氧器中的低壓飽和蒸汽由管道輸入余熱鍋爐低壓過熱器被加熱為0.4MPa、200℃ 的低壓蒸汽。流經調壓閥后經外部蒸汽管道供給用戶使用。汽包中的高壓飽和蒸汽由管道輸入余熱鍋爐高壓過熱器被加熱為1.6MPa、260℃的高壓蒸汽。流經調壓閥后經外部蒸汽管道供給用戶使用。如果有兩臺或三臺加熱爐,可以一臺加熱爐設置一臺余熱鍋爐;也可以多臺加熱爐共用一臺余熱鍋爐。即使一臺加熱爐檢修停爐,余熱鍋爐完全可以照常運行。因為余熱鍋爐可以在低負荷工況下運行。
為了縮短煙氣流程,減少風機電耗,引風機排出的煙氣最好不要回到原有煙囪,宜新建煙囪直接排放。